Get This Report about Indonesia Furniture Manufacturers
Table of ContentsGetting The Indonesia Furniture Manufacturers To WorkIndonesia Furniture Manufacturers for BeginnersThe Only Guide to Indonesia Furniture ManufacturersFascination About Indonesia Furniture ManufacturersNot known Factual Statements About Indonesia Furniture Manufacturers
There are some downsides to purchasing from a furnishings maker. For one, you may need to wait longer to obtain your furniture because it's being made to buy. Furthermore, you may not have the ability to see or touch the item prior to you buy it. A furnishings store is a firm that markets furnishings made by various producers.When you acquire from a furniture store, you're buying a piece of furniture that's already been made and prepares to be shipped to your home. One of the advantages of purchasing from a furnishings retailer is that you can usually see and touch the product prior to you buy it.
At BH Furnishings, we believe in establishing new criteria for excellence in the production of commercial furnishings - Indonesia furniture manufacturers. Our dedication to technology has actually led us to embrace cutting-edge automation innovation, changing the means we make furniture and moving us to the forefront of the sector. Gone are the days of hand-operated labor dominating the manufacturing flooring
Our machinery works flawlessly, assisted by the exact specifications set by our competent designers, guaranteeing regularly premium output. Claim farewell to manufacturing hold-ups and overtime expenses. Our automated systems operate relentlessly, 24/7, assuring a constant and continuous process. This means we not only satisfy but surpass shipment deadlines, providing our customers with a degree of integrity that typical manufacturing techniques just can't match.
Indonesia Furniture Manufacturers Can Be Fun For Everyone
Our manufacturing capability has risen, allowing us to fulfill the demands of even the largest projects without endangering on top quality. As your companion in business furniture options, we can effortlessly scale our result to accommodate your demands, no issue the scale. While traditional production relies heavily on manual work, our automated systems have actually significantly lowered our reliance on a large workforce.
Furnishings production is a complex process that entails various phases, from developing and product option to production and setting up. At each phase, there is an opportunity of issues or errors that can compromise the quality of the end product. To guarantee that furnishings is of excellent quality, furniture suppliers execute quality assurance procedures to determine and fix any kind of issues that may arise during manufacturing.
The examination procedure ought to cover numerous aspects, such as setting up, coating, colour, design, packaging, labelling, and marking. By executing an extensive evaluation process, manufacturers can guarantee their products fulfill the necessary high quality, safety, and toughness demands. They likewise supply the adaptability to deal with problems and make modifications before finishing the end product.
The procedure starts with the basic materials assessment to the last assembly of the furnishings. The goal is to make certain that the products are devoid of flaws, safe, and satisfy the consumer's expectations. Furnishings quality criteria are sets of standards and needs for furnishings production. They define the called for quality degree of furniture manufacturing and cover facets such as security, longevity, strength, and ecological effect.
The Single Strategy To Use For Indonesia Furniture Manufacturers

To guarantee their furniture items can endure various climate aspects, including sun, rain, snow, and wind, suppliers should think about worldwide identified standards that consist of examinations and testing. Right here are some of the requirements to remember: ASTM F1561-03 is a worldwide common established by the American Area of the International Association for Screening Materials (ASTM).
AFNOR try this web-site NF D60-300 is a safety and security conventional established by the French Standardisation Association (AFNOR) for outside seats and tables made for kids. The typical outlines safety and security demands and examination treatments. UL 962 is a global security standard created by Underwriters Laboratories (UL), an independent worldwide supply browse around here safety services firm. The basic relates to house and commercial home furnishings, consisting of outdoor furniture.
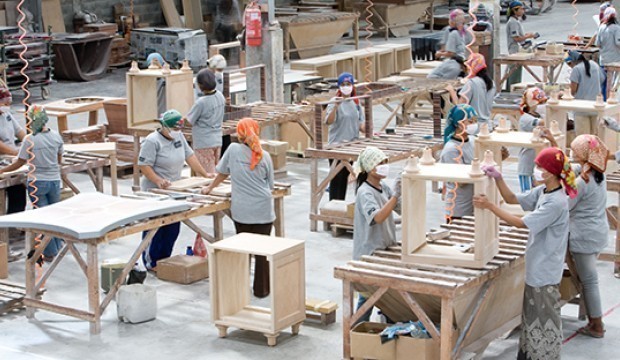
Getting The Indonesia Furniture Manufacturers To Work
It aids to identify flaws in the furniture and evaluate its efficiency and compliance with the called for quality criteria. These examples typically stand for the various kinds of furniture that they produce.
This might entail a mix of various examinations, including stamina testing, sturdiness testing, safety testing, and ecological impact screening. The examples are then checked for different quality criteria, such as toughness, toughness, safety and security, and environmental influence. The outcomes are after that examined to identify whether the products meet the called for quality requirements.
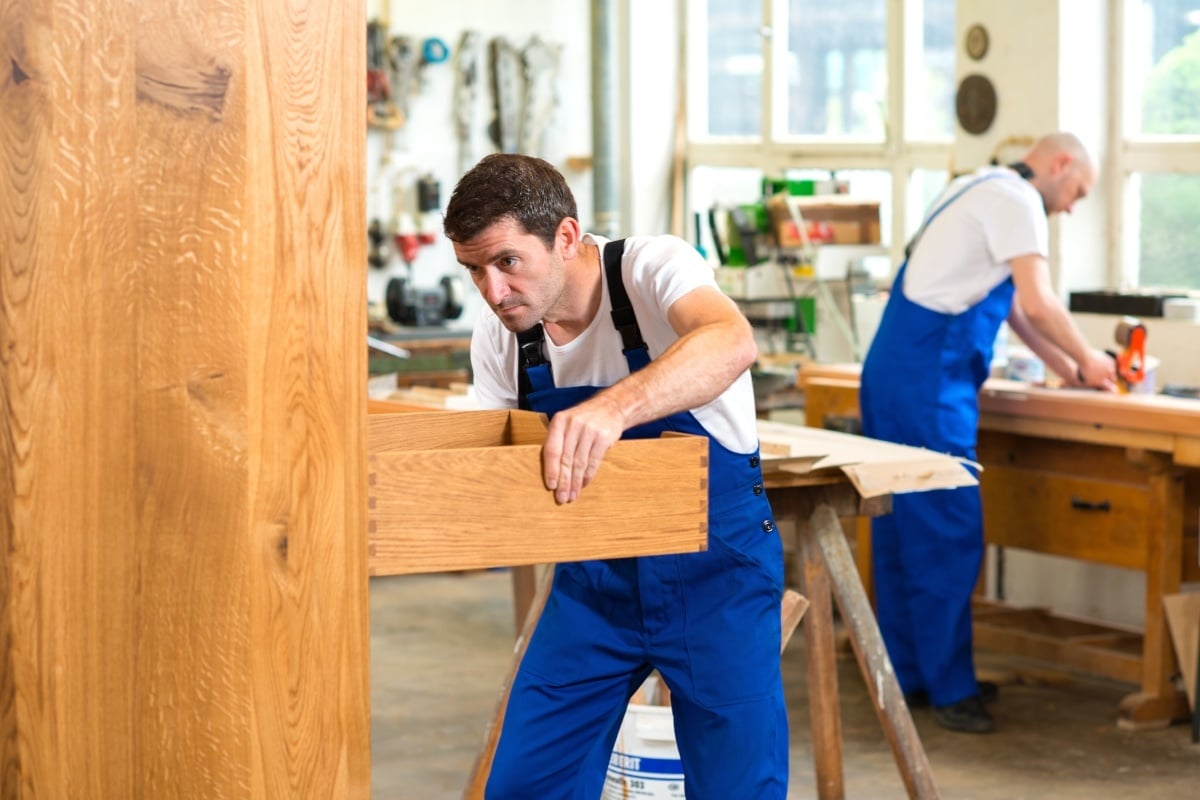
Typically, every retail shop furniture is various. Layouts meeting client benefit Taking full advantage of space use in storage space, screen, footfall, guest seating and walkways Making certain convenience of accessibility to items for tests and purchase Designing modular furnishings that is very easy to relocate and renovate Satisfying security demands of clients A quick TAT from layout to production and installation with minimal errors can assist resolve the above problems.
Getting The Indonesia Furniture Manufacturers To Work
A designer can understand the market trends and be ready with innovative designs in advance of time. Review right here: How DriveWorks Aids You to Reduce Preparation in Production Designers usually need to change the forms and dimensions of furniture at a moment's notification. These may have different visual and useful needs like front desk, and servicing desk that differ in dimensions.
Enhances item quality and check out here lowers scrap. Field instruction records along with amount launches are likewise generated for retail store furniture setups. Design models and conflicts are decreased, and the store flooring can begin manufacturing on the day of sales.
It is a highly affordable market, with companies aiming to keep up with changing consumer needs and the latest technical patterns. Today's consumers are a lot more likely to favor furniture that is tailored and made with sustainable products.